rTPC Industrialisation
Industrialisation of lab-scale recycling processes for ThermoPlastic Composiets
Summary
Recently recycling technologies for thermoplastic composites have been developed at lab-scale in the TPAC by the research group Lightweight Structures. R&D in a.o. the RAAK PRO project 'TPC-Cycle' have resulted in successful real-life demonstrator products, like the access panel door as developed for GKN Fokker. However, the TRL level of the developed principles are not yet applicable in industrial environments. Much more R&D needs to be done to industrialize processes and validate the principles on thermoplastic composites with different matrix and fibre materials.
One of the interested parties in this technology is Covestro Deutschland AG, being the partner in this project. At first instance, Covestro will bring in two types of waste material from their PC-carbon material Maezio®.
In the lab of the ThermoPlastic Composites Application Center (TPAC), the Lightweight Construction research group conducted research into the application, automation and recycling of thermoplastic composites (TPC). It has a wide range of test and production resources to carry out this research. In the long term, TPC offer particularly interesting application possibilities because of the enormous weight savings, corrosion resistance, weldability and impact resistance, but also because of the possibilities for producing large series of lightweight products at a low cost price repeatedly. Mobile applications such as those in the automotive industry also offer a potential growth market. For recycling of TPC, a completely new recycling process has been developed at lab-scale in the RAAK PRO TPCCylce project. This process is illustrated in below exhibit. By appropriately shredding the material, an acceptable fibre length is retained. Also, for further processing, a dedicated heating process was developed at lab scale, in order to minimise shear stresses that cause fibre breakage in usual processes and even disentangle fibres from woven laminates during heating. As a result, material performance in new products is optimised. The results obtained from the projects so far, encourage the TPAC to carry out further research in order to make technologies suitable for industry.
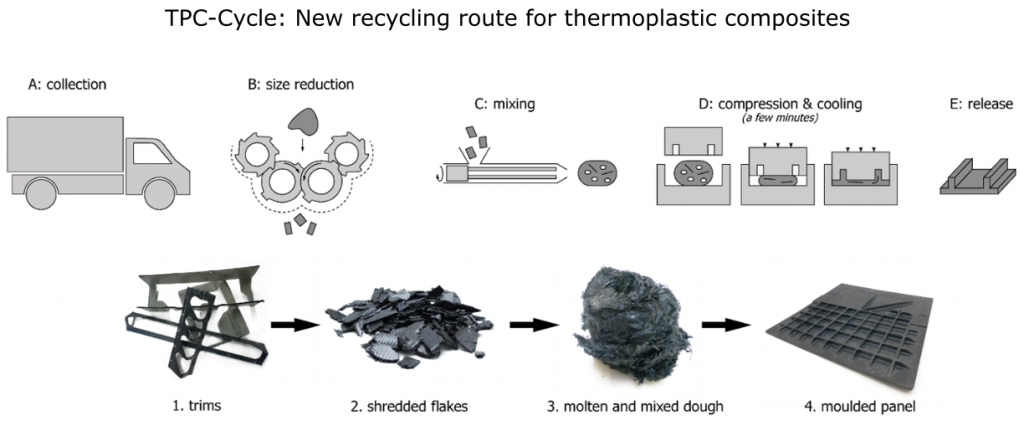
Industrial waste is generated during start-up of the production lines and as scrap of cut offs in composite production industries. Large volumes of materials with intrinsically near virgin quality are therefore disposed of before it was ever used in applications. The projected growth of TPC industry will result in a substantial
increase of these volumes in the near future. The TPAC has developed recycling technologies at lab scale, which could potentially introduce circularity for these materials. However, this technology has not yet been validated for application at an industrial scale. More research is needed for that. The TPAC wants to research this potential opportunity, while involving students. If successful, obtained knowledge will be of high value for education, students and the market. The objective of this project is therefore to validate the developed recycling technologies and make a next step into industrialisation. In this project collaboration is found with Covestro, using their material Carbon-PC. The main research question is:
To what extend can TPC recycling technology at labscale be made suitable and applicable for TPC materials in an industrial environment?
Underlying this objective are the following sub-questions:
a) Can consolidated plate cut-offs (in this project: Carbon/PC) be recycled with developed lab technology?
b) Can production waste (in this project: Carbon/PC) tape with varying matrix content be recycled with developed lab technology?
c) To what extend can this technology be standardised for industrial conditions, in terms of reproducibility, stability and robustness (considering possible contaminations as well)?
Project partners
Covestro
Duration
16 months, Start in November 2020
Funding
Partly financed by Tech For Future, Centre of Expertise HTSM Oost.
For more information about this project, please click here.