The project is investigating the possibility of using lignin and cellulose for 3D printing. With only these two materials it turned out not to be possible to print properly. Therefore, the bio-based polymer PLA (from corn starch) was used as a binder. The PLA is essential to get enough material into the flow for controlled extrusion.
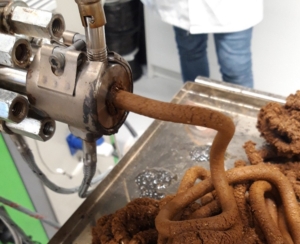
First tests on an extruder using a compound of PLA, lignin and cellulose.
In other experiments it has surprisingly been shown that lignin and cellulose from wood fiber can be pressed into a plate or other shapes. High pressure and high temperature are required to get cellulosic fibres into a matrix of lignin which result in mechanical properties comparable to HPL (high pressure laminates). Because with 3D printing the material is usually immediately bound to the atmosphere after extrusion, it is impossible to continue to exert pressure on the material after printing.
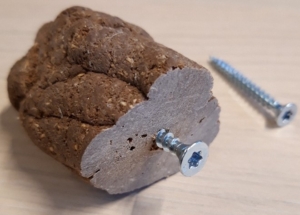
The printed sample on the left was tested for the ability to insert screws.
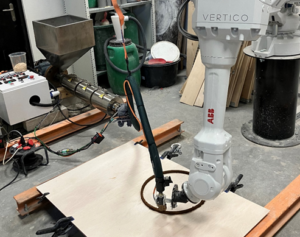
Setup of 3D-printing: the material leaves the extruder via a heated hose. The end of the hose (the nozzle) is attached to the robot arm.
Many different partners are part of the project, contributing various research questions. With these questions in mind, the project team worked with the companies in question to develop a concept for 3D ‘wood’ printing. These were first produced on a small scale, to verify that the designs meets the partner’s demand. These designs were then produced in full format with a large scale additive manufacturing printer, mounted on a robotic arm.
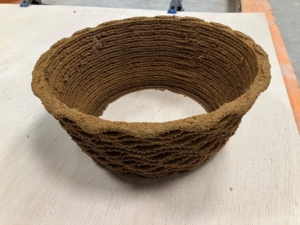
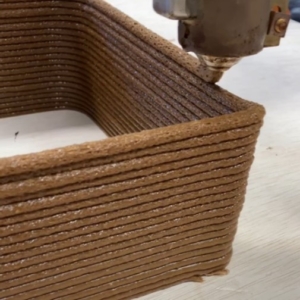
Examples of 3D-printed-wood objects.