New opportunities for application rejected production material
CompTape, a Dutch supplier of thermoplastic composite tape, was looking for a solution to also enter the market for compression moulded products in the composite world and, at the same time, find a sustainable destination for its rejected material. This company now supplies glass fiber reinforced plastic ‘tape on the roll’ that is being used for example for making pressure vessels. When asked whether this so called ‘continuous material’ also could be used as a raw material for compression moulded products, Saxion’s TPAC was asked for research and advice. Now that this research has been completed, the conclusion is that this indeed is possible – and also in a competitive way.
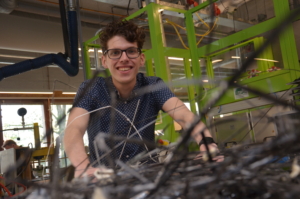
Robin Derikx: “The result of the research is relevant for the industry.”
With this addition to its product range, CompTape can significantly increase its sales opportunities because compression moulded products form a different, perhaps larger, market than tape. In addition, this could also be a solution for the reuse of any off-specification material and rejections. This material does not have to be thrown away and this of course is of great importance on the way to circularity. In addition, the tape on the roll is relatively price efficient and because of this, the manufacturer can also use already manufactured tapes.
By cutting both this continuous material and any off-specification material plus rejects into pieces, sufficient amount of the desired base material is available for compression moulding products. In this way, pieces of tape of different lengths, for example 10, 20 or 25 millimeters, are produced, which can then be mixed with a plastic as matrix. This resulting material then forms the raw material for all kinds of different press products.
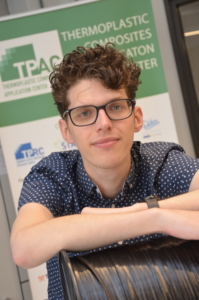
Robin Derikx: ‘I can draw the preliminary conclusionthat the composite material of cuttape gives slightly better results than acommonly used industrial alternative’
Student assignment
TPAC looked at this case and gave Robin Derikx (Mechanical Engineering student at Saxion University of Applied Sciences) for his graduation the assignment to investigate the possibilities. Derikx also had to examine whether the properties of the new composite corresponded with what is already available in the market so that CompTape can estimate the market opportunities in this way.Professor Ferrie van Hattum of TPAC supervised this research and is enthousiastic about the result. “Robin Derikx has carried out a sub-trajectory within CompTape’s plan that looks at what to do with the production surplus. We have developed something for them and Derikx has done well. It is a good example of applied research.”
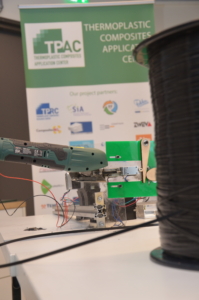
Ferrie van Hattum, professor Lightweight Structures: “Good and practically relevant work by the graduate.”
Cutter
To graduate, Robin Derikx was looking for an assignment in the direction of design, construction and choice of materials. “That’s how I ended up at TPAC, initially to design a cutter for this composite tape. I developed a tool but after a few weeks it became clear that the cutter as such could only be part of the research. Then I switched from a construction topic to the research topic Micromechanical Properties of Composites. ”The cutter was therefore phase one and the second phase of the research consisted of making mathematical models. “This was used to calculate the consequences for the micro-mechanical properties as a result of varying fiber lengths and mixing ratios between those fibers and the plastic matrix. With the help of the mathematical models I have sketched an expectation pattern. After that I started with the actual physical cutting of the tapes and with determining how much fiber you actually need and how much matrix you need to mix exactly for the right properties. Together with Ilse ten Bruggencate and Remi Hoefman from TPAC, I carried out this research up to and including the compression moulding of composite panels. I then took samples from those panels in order to be able to do the necessary bending and impact tests. ”
Mechanical engineering and TPAC: advanced materials
Robin Derikx studied Mechanical Engineering at Saxion University of Applied Sciences. Within the school, this program works together with three research groups, including Lightweight Structures. ME team leader Lando Lemmers says: “One of the pillars of our training is Construction Material and Production and the Lightweight Structures research group fits in very well with this. We have also set up a minor called AMPE, which stands for Advanced Materials and Production Engineering and this includes working with fiber-reinforced plastic. The minor also includes a practical within the TPAC. ”The link between the training and the TPAC is important, says Lemmers. “The first two years of the Mechanical Engineering training mainly consist of standard subjects, but for the second year we now have a practical injection molding, the most common mechanical processing method for plastics, through a collaboration with TPAC. Here the research group helps us and vice versa.”
Design or research
The Mechanical Engineering program offers two options for graduating, namely with a design or with a research project, and the latter of course fits very well within a research group. Lemmers: “We now have several graduates at Lightweight Construction. It now concerns two or three students a year and this is a small proportion of a total of sixty to eighty ME graduates. But it’s a start and it will grow.”
Intensify cooperation
The growth of the TPAC at Ariënsplein in Enschede is clearly visible, only a few years ago TPAC started to operate at this location and it is now packed with equipment and materials and there is a lively dynamic with researchers, students and trainees. The now positive attitude of the Mechanical Engineering program and the growth of the research group will intensify the collaboration between both parties. The number of students graduating from TPAC will certainly increase.
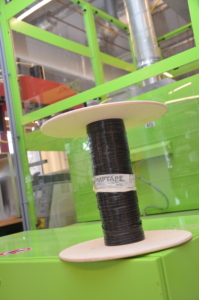
Consistent data
All the results of those tests have been incorporated into graphs and tables and from there the results have been compared with the expectations of the theoretical model. Derikx: “This model turned out to be quite correct, apart from the fact that the model obviously does not take into account the things that can simply go wrong in practice, with the machine and the process. But in essence, the data obtained were consistent enough to say that the practical trials followed what the theoretical models predicted. ” Derikx therefore says that he can also draw ‘the preliminary conclusion’ that the material of the cut tape actually produced slightly better results than a composite material that is already used in the industry and that is manufactured on the basis of exactly the same material, but that is offered in granular form. “This fact is relevant for the industry because this material is used quite a lot. ”
Impact with applied research
Professor Lightweight Structures Ferrie van Hattum is director of the TPAC. “Our primary goal is to conduct industrially relevant applied research; in our case, this translates into the research projects we run with companies and other institutions. We also want these activities to have an impact on society and education. To this end, we involve students in our projects and vice versa, we want to feed the newly acquired knowledge back to education. We contribute to the minor in the Mechanical Engineering program and we provide a module in the Master of the Textiles program in which students learn about composites. Or students follow an injection molding practical with us. Finally, the bodies that finance a large part of the research, the university of applied sciences and the government, want to see that we can demonstrate a certain level of knowledge. In scientific research, you measure this, for example, by the number of scientific publications that you generate. But we do applied research and that really is different from scientific research, so it cannot be done this way. As head of the research group, I therefore translate this requirement into the amount of research projects awarded and the overall participation in them by companies and other institutions. This is only possible at a significant level if your knowledge development is up to standard.”